A Comprehensive Overview to the Process and Advantages of Plastic Extrusion
In the large realm of manufacturing, plastic extrusion arises as a very efficient and essential procedure. Transmuting raw plastic into continuous profiles, it provides to a variety of sectors with its amazing flexibility.
Recognizing the Basics of Plastic Extrusion
While it might show up complex in the beginning look, the process of plastic extrusion is fundamentally easy - plastic extrusion. It is a high-volume manufacturing strategy in which raw plastic is thawed and shaped into a constant profile. The process starts with the feeding of plastic product, in the type of pellets, granules, or powders, right into a warmed barrel. The plastic is after that thawed making use of a mix of warmth and shear, applied by a turning screw. Once the molten plastic reaches the end of the barrel, it is compelled via a small opening called a die, shaping it right into a desired kind. The shaped plastic is after that cooled, strengthened, and reduced into wanted lengths, completing the process.
The Technical Refine of Plastic Extrusion Explained
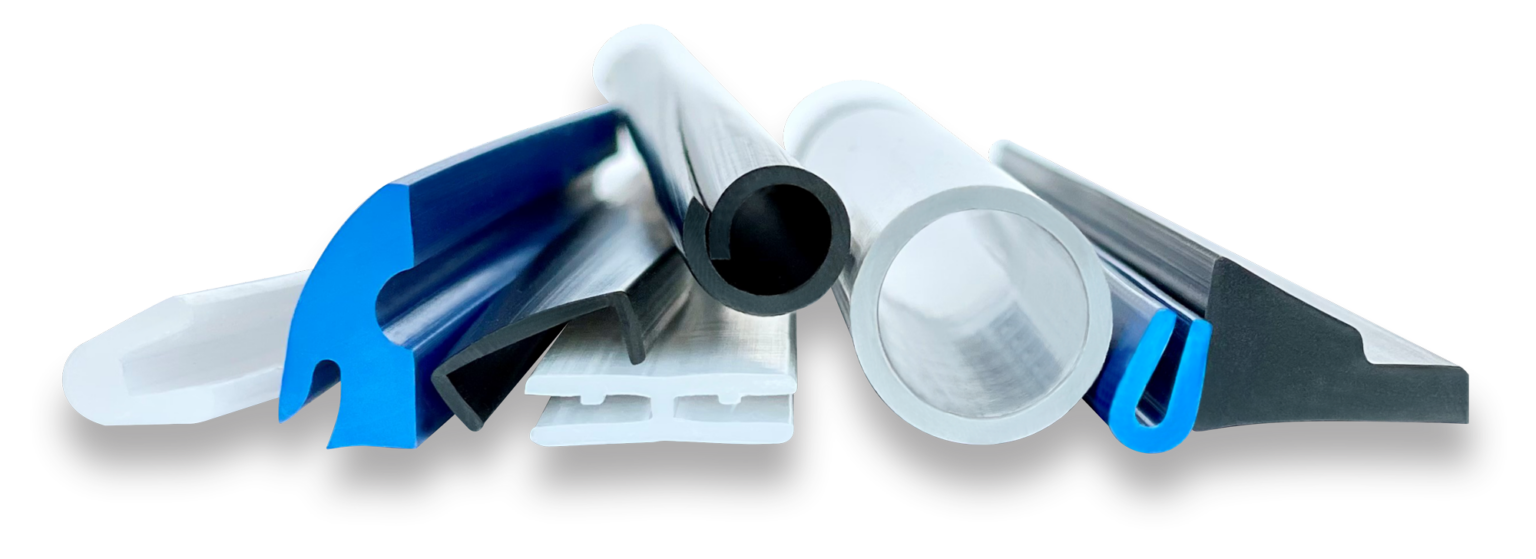
Kinds Of Plastic Suitable for Extrusion
The selection of the best type of plastic is an essential facet of the extrusion procedure. Numerous plastics use unique residential properties, making them extra suited to particular applications. Polyethylene, for instance, is typically used due to its inexpensive and simple formability. It supplies excellent resistance to chemicals and wetness, making it suitable for products like tubing and containers. Likewise, polypropylene is an additional preferred option as a result of its high melting point and resistance to tiredness. For more robust applications, polystyrene and PVC (polyvinyl chloride) are commonly picked for their strength and toughness. Although these prevail alternatives, the selection eventually depends on the certain demands of the product being produced. Comprehending these plastic types can substantially boost the extrusion process.
Comparing Plastic Extrusion to Other Plastic Forming Techniques
Understanding the kinds of plastic suitable for extrusion leads the method for a wider discussion on just how plastic extrusion piles up versus other plastic developing techniques. Plastic extrusion is unparalleled when it comes to producing continual profiles, such as seals, pipes, and gaskets. It also allows for a consistent cross-section along the size of the item.
Key Advantages of Plastic Extrusion in Manufacturing
In the world of manufacturing, plastic extrusion supplies many considerable benefits. One notable advantage is the cost-effectiveness of the process, which makes it a financially appealing manufacturing technique. In addition, this strategy offers premium item adaptability and improved production rate, consequently enhancing total production performance.
Cost-Effective Production Technique
Plastic extrusion leaps to the leading edge as an affordable production method in manufacturing. Additionally, plastic extrusion needs much less energy than standard production methods, contributing to reduced operational prices. In general, the financial advantages make plastic extrusion a very appealing option in the production sector.

Superior Product Flexibility
Beyond the cost-effectiveness of plastic extrusion, one more significant advantage in producing lies in its remarkable item adaptability. This procedure enables the development of a broad selection of products with differing dimensions, designs, and forms, from simple plastic sheets to detailed profiles. The versatility is associated to the extrusion pass away, which can be tailored to produce check out this site the desired product style. This makes plastic extrusion an ideal service for sectors that call for tailored plastic parts, such as auto, building, and packaging. The ability to create varied items is not just helpful in conference particular market needs but likewise in allowing manufacturers to discover brand-new line of product with marginal capital expense. Essentially, plastic extrusion's item versatility fosters development while improving operational effectiveness.
Boosted Manufacturing Rate
A substantial benefit of plastic extrusion exists in its improved manufacturing speed. Couple of various other manufacturing procedures can match the speed of plastic extrusion. In addition, the capability to maintain constant high-speed production without giving up item top quality sets plastic extrusion apart from other techniques.
Real-world Applications and Influences of Plastic Extrusion
In the world of manufacturing, the technique of plastic extrusion holds profound learn the facts here now relevance. This process is extensively utilized in the manufacturing of a selection of products, such as plastic tubes, home window structures, and weather removing. As an outcome, it considerably influences fields like building, packaging, and auto sectors. Its impact expands to day-to-day things, from plastic bags to toothbrushes and disposable cutlery. The economic benefit of plastic extrusion, mainly its affordable and high-volume result, has actually reinvented manufacturing. Nevertheless, the ecological impact of plastic waste remains a problem. The industry is constantly making every effort for advancements in recyclable and naturally degradable materials, suggesting a future where the benefits of plastic extrusion can be retained without endangering environmental sustainability.
Final thought
In conclusion, plastic extrusion is a very effective and reliable approach of transforming resources right into diverse products. It provides countless benefits over various other plastic creating techniques, consisting of cost-effectiveness, high result, minimal waste, and design versatility. Its effect is exceptionally really felt in numerous industries such as building and construction, automotive, and customer items, making it a critical process in today's production landscape.
Digging much deeper read more right into the technological procedure of plastic extrusion, it begins with the choice of the proper plastic material. Once cooled down, the plastic is cut right into the needed sizes or wound onto reels if the product is a plastic film or sheet - plastic extrusion. Contrasting Plastic Extrusion to Other Plastic Forming Methods
Recognizing the types of plastic appropriate for extrusion leads the means for a more comprehensive discussion on just how plastic extrusion piles up against various other plastic forming approaches. Couple of other manufacturing processes can match the speed of plastic extrusion.